For most film photographers, processing your own film can be intimidating. That’s why I was excited to try the AGO Film Processor. Here’s what I found in a nutshell:
Simple to Use: No complex settings here. The AGO Processor has clear buttons for different film types. Set the correct process times for each step, fill the tank, set it going, drain the tank, repeat with the following step, and relax!
Compact Size: This processor won’t take over your darkroom. It’s small enough to store easily, which is perfect for limited space.
Reduced Chemical Consumption: The horizontal position needs less chemicals: The standard Paterson 2 reel tank only needs 350ml versus 580ml when used vertically with stick agitation
Consistent Results: I’ve processed several rolls of color and B&W film now, and the negatives have come out great every time. The constant agitation ensures even development while the processor compensates for the dropping temperature.
Downsides: It might not be for everyone. If you want super precise temperature control, this might not be the best option. Also, filling the tank takes a bit more time while you need to get used to draining the tank with the processor attached. This makes it less suitable when developing a large number of films.
Overall: The Visual Vintage AGO Processor is a fantastic choice for photographers who want to take control of their film processing without breaking the bank. It’s easy to use, reliable, and frees you from lab turnaround times. Highly recommended!
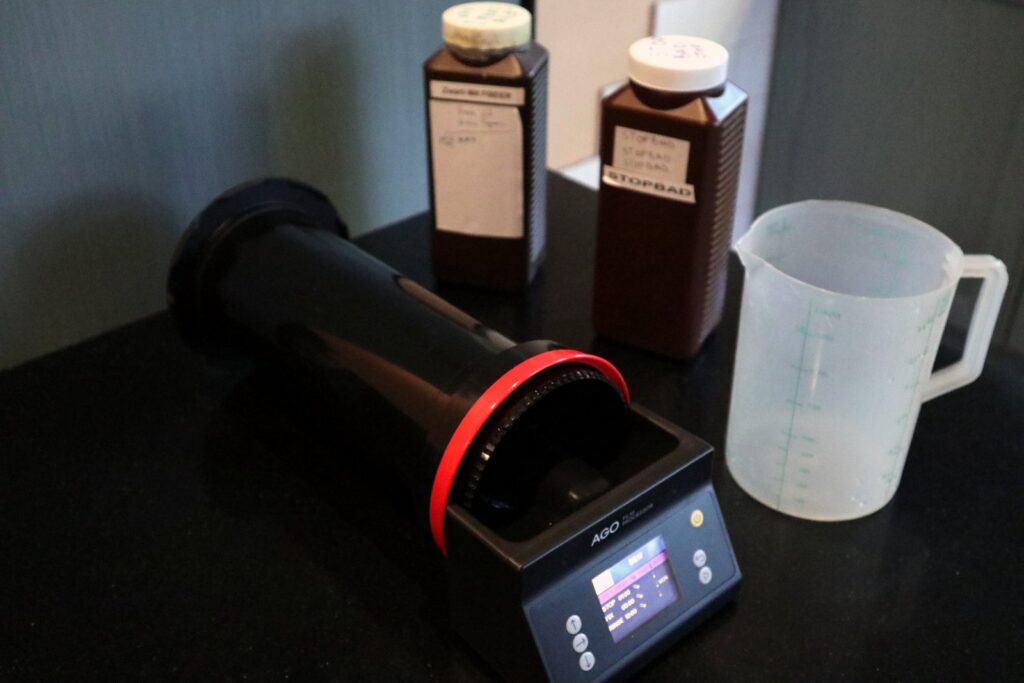
Comprehensive review
Nowadays, the analogue photography market is growing and growing. More and more people want to develop their own films. There are various reasons for this. To name only a few: there is the short turnaround time, it is often cheaper to do it yourself and last but not least: for many people, it is a very rewarding part of the analogue photography process.
Black and white processing is usually done at room temperature and does not require constant agitation. When developing colour film, temperature control can be a problem. Colour processes are optimised for continuous agitation at a constant temperature. Vintage Visual came with a great concept to avoid the hassle of a constant temperature water bath, combined with continuous agitation. The AGO processor does not heat up the chemicals, so you need to do that yourself before you begin.
To compensate for the temperature drop of the developer and other process chemicals, you can make the process time longer. How much longer is often a guess but for this, the AGO film processor has a built- in compensation table for various developer processes. More about that later in this review.
How does it work?
Most people who develop their own films are familiar with the concept of winding film on a reel, placing it in a round tank that stands up, pour in the developer, start the timer, agitate by rotating the reel in a certain sequence, and then pour the developer out after the time has finished. This procedure is then repeated for the other process steps and finally, the film will be rinsed and hung to dry.
The AGO processor uses a Paterson System 4 tank with a stand attached to the bottom side and the AGO processor placed at the Funnel side. The processor has a motor that couples to the core of the tank and a thermocouple that measures the temperature of the fluid in the tank. The funnel is modified with 3 holes to accommodate pouring in the liquids. The horizontal position allows the use of less volume for the chemicals because the continuous agitation provides constant wetting of the entire film. It also makes sure that the thermocouple is in constant contact with the liquid to monitor the actual temperature. This temperature is fed into the controller that is programmed to compensate for the temperature when it drops over time. Each step in the process can be adapted to compensate for this temperature by shortening the time when the initial temperature is too high or extending the time when this temperature is too low. This is a continuous process during the entire step. For Black and White film processing it is recommended to shorten the development time by 15%, a value that did work for me. Although I did not try it, the processor can be programmed to use intermittent agitation with the tank standing up. Of course, you will then need to fill the tank with the standard minimal amount of liquids as printed on the bottom of the Paterson tank.
The reduced chemical consumption comes with a big bonus, especially for people who develop their own colour films: The 5-reel Paterson tank only needs 650 ml of fluid to process 5 135 reels or 3 120 reels! Since most C41 users will buy and make up sets for 1 liter of fluids, they could not use this tank to the fullest, but now they can!
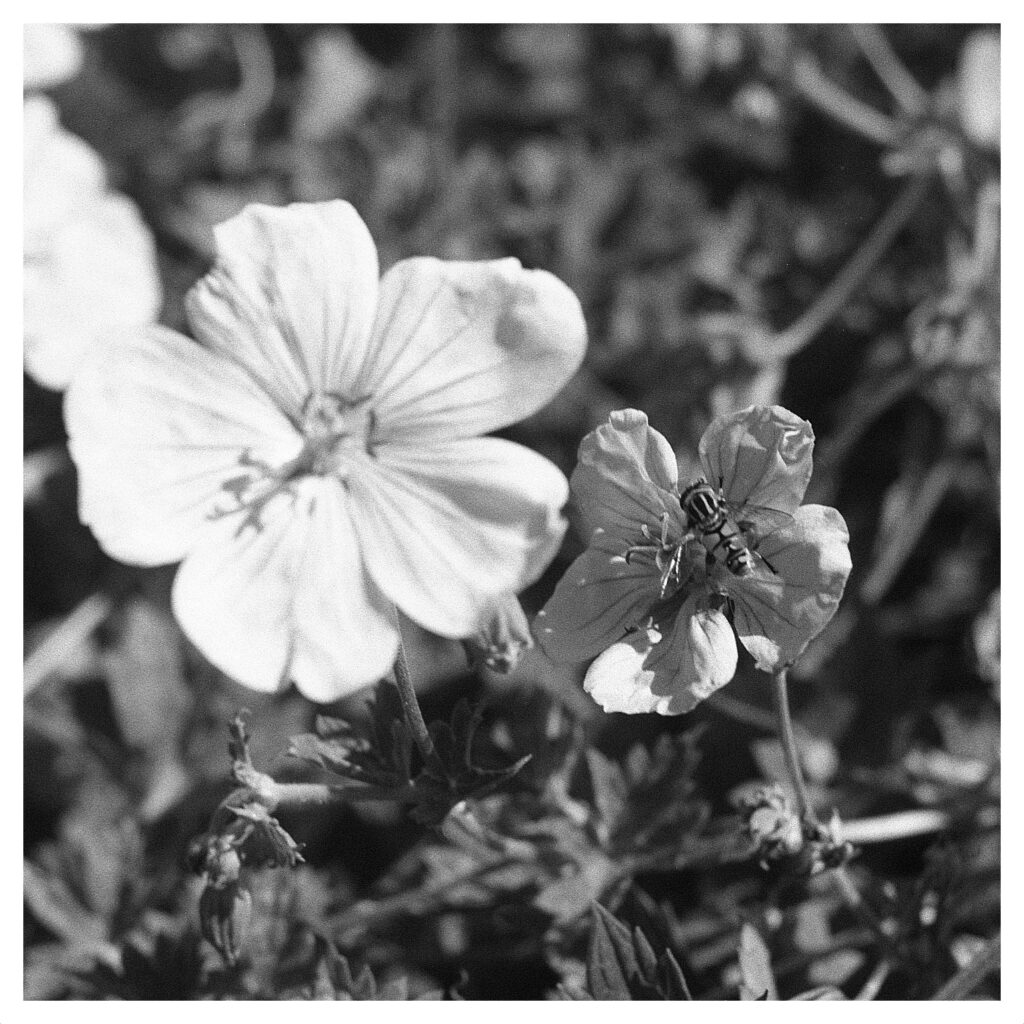
Time compensation
The AGO processor is programmed with various compensation graphs for different types of chemicals: For Black and white film processing, the compensation is aligned with the Time/Temperature chart as published by Ilford. This can be used for all “normal” Black and white film development. for B&W – Cinestill DF96 there is a separate program. Each type of color chemical (C-41, E-6, ECN-2, RA-4) has its own compensation graphs adapted to the specific requirements of color film development.
Included are: C-41 – Tetenal, C-41 – Cinestill, C-41 – Arista Unicolor, C-41 – Bellini E-6 – Cinestill D6 E-6 – Arista and ECN-2 – Cinestill. Future updates can be downloaded from the AGO support page.
Custom programs can be entered into your machine via AGO’s web interface when connected to WiFi. This will further enhance the ease of use of the processor. I did not need to use this. For all the processing I did I could reprogram the generic settings for Black and White film and for C-41, the Bellini settings are already in the processor.
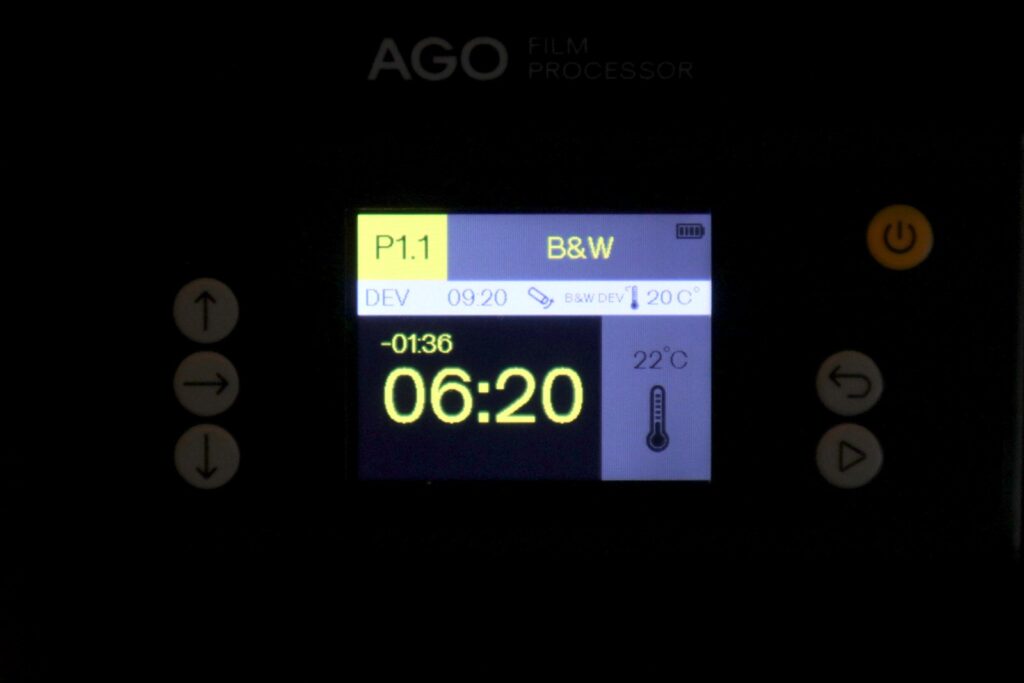
Real user experience
For this review, I processed different sizes of film starting with the standard Paterson tank that came with the AGO processor.
I started with a single roll of B&W 135 film applying the -15% compensation for the continuous agitation.
The result was very good although denser than my normal developing result. But all shadow detail was there and negatives could be scanned without problem.
Then I processed a B&W 120 film with the same compensation with good results.
The third film was a 220 format B&W film and that came out very good as well, convincing me that the -15% compensation is a good starting point.
With these three films, I found it difficult to mount the processor on top of the tank. Aligning the drive shaft with the inner core was difficult and took several efforts to align correctly with the holes in the funnel. Luckily the AGO forum on Facebook helped me out when mentioning this. Instead of mounting it while the tank was standing vertically, I should keep it more or less horizontally and push the tank onto the processor. This did the trick.
Then I decided to process C41 colour film: Two 135 colour films in the standard tank with Bellini C41 kit which uses separate Bleach and Fixer. Starting temperature of the developer was 40 degrees C. The processor prolonged the time with 10 seconds to compensate for the drop in temperature ending slightly below the recommended temperature of 38 degrees.
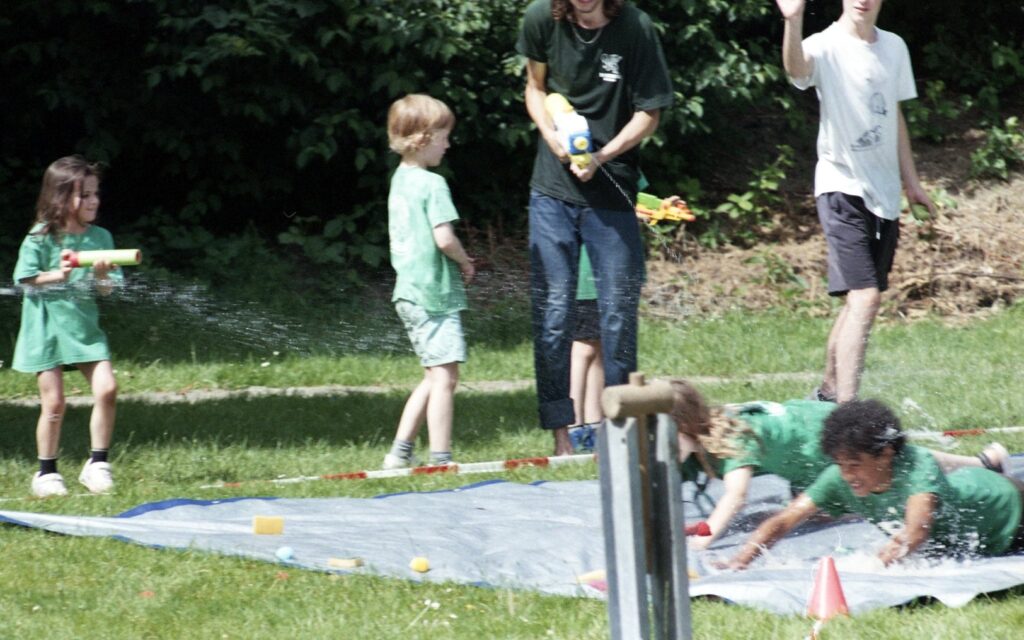
Here the first slight drawback of the system came forward.
Bleaching time is only 45 seconds, followed by a short Fixing time of 90 seconds. Pouring in the chemicals and emptying the tank takes relatively much time. Luckily, the process times can be longer for bleach and fix but for me it was a bit nerve wrecking operating like this. A two bath processing kit might be more suitable for use with this processor.
This did not put me off, and I developed another C41 film. This time with slightly colder chemicals and a lower room temperature. The processor compensated in 2 steps during processing with a total of 51 seconds. I now got more used to emptying the top heavy tank and this film came out beautifully as well.
After this session, I decided to use my 5-reel Paterson tank. I changed the original funnel for the funnel with the three holes and developed two 120-format B&W films.
The environmental temperature was higher this time and I started with a developer temperature of 21 degrees C. The set time was 9m20s which was corrected by the processor with -57s to correct for the higher temperature. And these two films came out very nice as well.
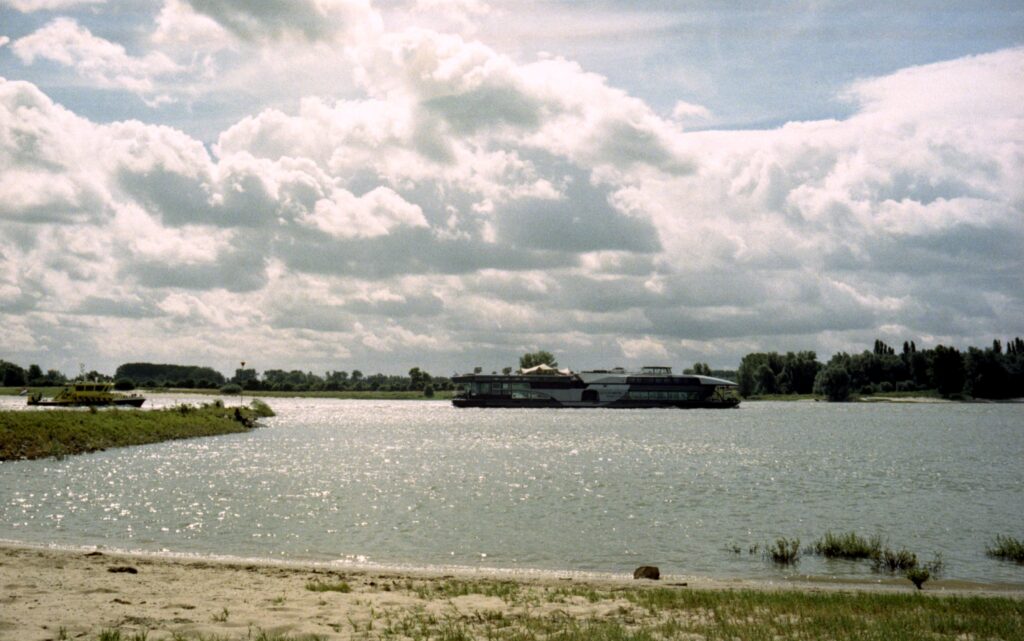
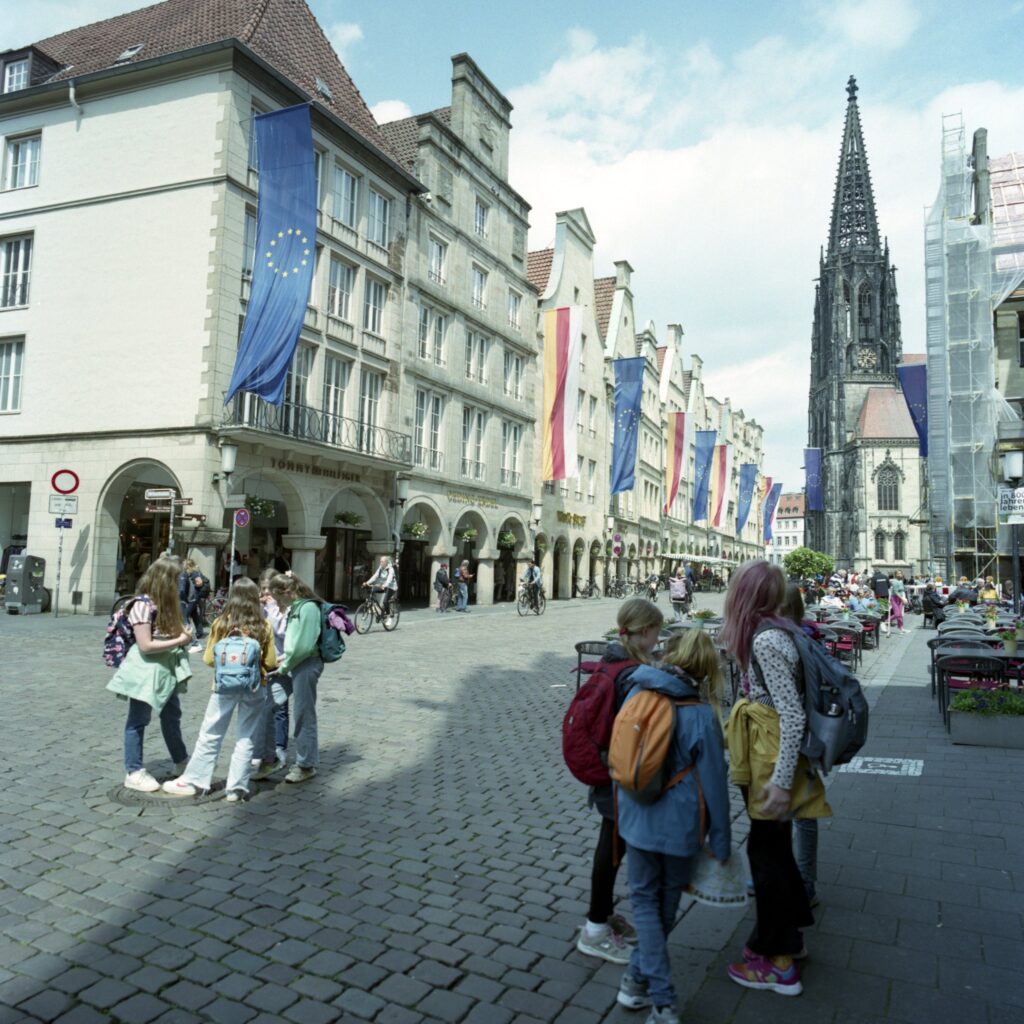
Verdict
-
- The temperature compensation works very well for both B&W and C-41 processing.
- Continuous agitation with time compensation works fine as well, but maybe you have to tweak the compensation to suit their taste.
- Handling the tank with the processor mounted on top takes time to get used to when emptying chemicals.
- One has to be more careful with pouring in chemicals since the funnel capacity is lower because of the mounted processor.
- Luckily, the smaller amount of chemicals to process more than one film at one time, does compensate this a bit in time. (When processing only one 135 film in a Paterson tank requires 290ml of liquid while the standard tank used horizontally requires 350ml for either one or two films)
- It takes up less space than a Jobo processor and compared with the CPE2 process I own, is less messy since the outside of the tanks stays dry with the AGO processor
- It is much more less expensive than even 2nd hand waterbath processors
- Since I use minimum amounts of chemicals I did not have any trouble with the leaking seal, but I will never the less replace it with the repair set AGO provides.
- The user manual could be a bit more clear on how to mount the processor on the tank.
- This is a good example of the commitment Vintage Visuals show to their customers. This is worthwhile since I intend to use this processor for all my development in the future.
Share this post:
Comments
Gary Smith on AGO Film Processor – An honest review of Vintage Visual’s Film Processor
Comment posted: 19/08/2024
Comment posted: 19/08/2024
Jeffery Luhn on AGO Film Processor – An honest review of Vintage Visual’s Film Processor
Comment posted: 19/08/2024
Thank you for such a clear and concise review. Well written! I developed my first roll of B&W around 1966 and have not seen any new processing machines I liked, but this one interests me! In all my years, I've often had either surge due to over agitation or bromide drag from stand development. This sounds like a way to get consistent results with less chemistry. I'm interested to see if they have a tank for processing 4x5. My Yankee tanks require 50oz for 12 sheets, and the pouring is a mess! Thank you for this article. I will check out this clever device.
Comment posted: 19/08/2024
Eric Rose on AGO Film Processor – An honest review of Vintage Visual’s Film Processor
Comment posted: 20/08/2024
Comment posted: 20/08/2024
James Billings on AGO Film Processor – An honest review of Vintage Visual’s Film Processor
Comment posted: 21/08/2024
I currently only do BW at home, and send colour off to a lab as I don't trust myself to be accurate with temperatures that I think C41 requires. This seems a good answer to that; but it's still quite the investment. Maybe one day...
Comment posted: 21/08/2024
Chris on AGO Film Processor – An honest review of Vintage Visual’s Film Processor
Comment posted: 27/08/2024
I got V1 for 199$ which is/was a bargain, and it works like a charm. It can also keep the temperatures of chemicals...